Description
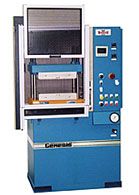
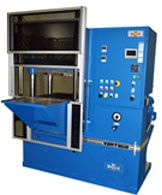
Genesis Presses
Ideal for Compression Molding of Rubber, Plastic, Composites and Laminating: In 15 to 150 Ton Capacities
Genesis Series Hydraulic Presses for Many Applications
Ideal for Compression Molding of Rubber, Plastic, Composites and Laminating: In 15 to 150 Ton Capacities
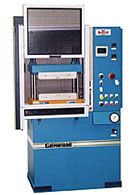
Genesis hydraulic lab presses are available in 15 through 150 ton capacities. The hydraulic system produces faster closing and opening speeds, making it ideal for use with many of today’s advanced molding compounds. Optional heated platens are available for 500°F, 800°F and 1200°F operating temperatures, which are required for many other applications.
Genesis Presses can be Customized for Compression Molding Applications:
While standard Wabash Genesis Presses handle a broad range of applications and can be upgraded or performance-enhanced with available options, your unique requirements may call for a “customized” press. Consult your Wabash representative for more information about “customization ” for your particular needs.
- Clamp forces available from 15 to 150 tons
- Adjustable daylight opening (daylight varies by model)
- Steel platens, machined flat and parallel within + .001” in/ft
- Platen size: 12″ x 12″ to 30″ x 30″
- Programmable controller with HMI
- Cycle counter thru PLC
- Automatic transition from closing to pressing speed
- Closing speed 70 IPM (approx.)
- Pressing speed 5 IPM
- OSHA approved operating system
- Pressure relief valve with analog pressure gauge
- Integral hydraulic system with high-efficiency TEFC motor, reservoir & water-cooled heat exchanger
- Clamp area guards with keyed interlock
- Electrical supply: 460/3/60 (other voltages available)
- Heated platens (to 500°F, 650°F, 800°F or 1200°F) with cartridge heaters
- Digital PID temperature controllers
- Programmable ramping controllers
- Programmable heating (and cooling) thru PLC, programmable thru HMI
- Water cooled platens
- Steam heated platens
- Oil heated platens
- Larger platen sizes
- Low pressure system
- Additional cylinder stroke
- Pressing speed control
- Contact gauge for quieter & more energy efficient operation
- Hydraulic part ejector
- High speed hydraulic package
- Digital display of clamp force
- Electronic force control
- Air-cooled heat exchanger
- WaterSaver valve for heat exchanger
- Down acting configuration (with Sitema safety catcher)
- Extended tie rods
- Work table
- Shuttle platens
- Lower sliding platens
- Tilting platens
- Mechanical eject
- Power operated safety gate (in lieu of standard manual gate
- Multiple daylights
- T-slots or tapped holes in platen for mold mounting
- 7 day timer for heaters
- Cycle counter (with keyed reset)
- Chart recorder Light curtains
- Light curtains
- Extra heat zones in platen(s)
- Audible or visual alarms
- Mold heat temperature controllers and plugs
- Clamp area lighting
- 220, 380 or 575 volt operation
- UL, CUL or CSA configurations available
- Smartdac Data Acquisition System
Vantage Presses
Ideal for Compression Molding, Bonding, Trimming and Laminating: 200 to 1000 Ton Capacities
Vantage Series Hydraulic Presses for Many Applications
Ideal for Compression Molding, Bonding, Trimming and Laminating: 200 to 1000 Ton Capacities
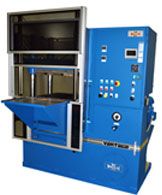
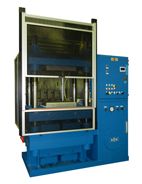
Energy-Efficient Hydraulic System – Integral hydraulic system features energy-efficient load-sensing pump and TEFC energy-efficient electric motor sized for the press. Components are easily accessible for quick maintenance.
User-friendly Controls — Programmable controller with interface controls press sequence. Digital temperature controllers maintain uniform temperature of optional heated platens.
Reliable Control Systems — NEMA-rated control cabinet designed for easy access.
Safety Guards — All new Wabash presses include a safety guard with keyed interlock around the molding area for improved safety. Sliding, hinged or power gates are available.
Vantage Presses can be Customized for Compression Molding Applications:
While standard Wabash Vantage Presses handle a broad range of applications and can be upgraded or performance-enhanced with available options, your unique requirements may call for a “customized” press. Consult your Wabash representative for more information about “customization ” for your particular needs.
- Clamp forces available from 15 to 150 tons
- Adjustable daylight opening (daylight varies by model)
- Steel platens, machined flat and parallel within + .001” in/ft
- Platen size: 15″ x 15″ to 48″ x 48″
- Programmable controller with HMI
- Cycle counter thru PLC
- Automatic transition from closing to pressing speed
- Closing speed 45 to 100 IPM (depending on model)
- Pressing speed 3 to 5 IPM (depending on model)
- OSHA approved operating system
- Pressure relief valve with analog pressure gauge
- Integral hydraulic system with high-efficiency TEFC motor, reservoir & water-cooled heat exchanger
- Clamp area guards with keyed interlock
- Electrical supply: 460/3/60 (other voltages available)
- Heated platens (to 500°F, 650°F, 800°F or 1200°F) with cartridge heaters
- Digital PID temperature controllers
- Programmable ramping controllers
- Programmable heating (and cooling) thru PLC, programmable thru HMI
- Water cooled platens
- Steam heated platens
- Oil heated platens
- Larger platen sizes
- Low pressure system
- Additional cylinder stroke
- Pressing speed control
- Contact gauge for quieter & more energy efficient operation
- Hydraulic part ejector
- High speed hydraulic package
- Digital display of clamp force
- Electronic force control
- Air-cooled heat exchanger
- WaterSaver valve for heat exchanger
- Down acting configuration (with Sitema safety catcher)
- Extended tie rods
- Work table
- Shuttle platens
- Lower sliding platens
- Tilting platens
- Mechanical eject
- Power operated safety gate (in lieu of standard manual gate
- Multiple daylights
- T-slots or tapped holes in platen for mold mounting
- 7 day timer for heaters
- Cycle counter (with keyed reset)
- Chart recorder Light curtains
- Light curtains
- Extra heat zones in platen(s)
- Audible or visual alarms
- Mold heat temperature controllers and plugs
- Clamp area lighting
- 220, 380 or 575 volt operation
- UL, CUL or CSA configurations available
C-Frame Hydraulic Presses for Many Applications
Ideal for Compression Molding, Trimming and Laminating of Longer Workpieces
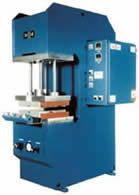
Wabash has extended the modular design concept to these versatile hydraulic compression presses with an open throat for greater flexibility in rubber molding, seam bonding, splice molding, encapsulating, trimming and laminating long work pieces.
Each machine can be configured to perform your precise task. Many options are available including heated platens. Individual temperature controllers and other options permit fine tuning of the performance of each press. Standard features on C-Frame hydraulic presses include heavy duty slab side construction with down acting cylinders. Precision ground steel platens are machined parallel and level within +/-.001 in/ft. for precise quality results.
An integral hydraulic system features a gear or variable volume, pressure compensated pump (varies by model). A pressure relief valve and gauge is included for adjustable clamp force.
C-Frame Presses can be Customized for Compression Molding Applications:
While standard Wabash C-Frame Presses handle a broad range of applications and can be upgraded or performance-enhanced with available options, your unique requirements may call for a “customized” press. Consult your Wabash representative for more information about “customization ” for your particular needs.
- Down acting configuration (with Sitema safety catcher)
- Clamp forces available from 15 to 100 tons
- Steel platens, machined flat and parallel within + .001” in/ft
- Platen size: 15″ x 15″ to 30″ x 30″
- Programmable controller with HMI
- Cycle counter thru PLC
- Automatic transition from closing to pressing speed
- Closing speed 70 to 100 IPM (depending on model)
- Pressing speed 5 IPM
- OSHA approved operating system
- Pressure relief valve with analog pressure gauge
- Integral hydraulic system with high-efficiency TEFC motor, reservoir & water-cooled heat exchanger
- Clamp area guards with keyed interlock
- Electrical supply: 460/3/60 (other voltages available)
- Heated platens (to 500°F, 650°F, 800°F or 1200°F) with cartridge heaters
- Digital PID temperature controllers
- Programmable ramping controllers
- Programmable heating (and cooling) thru PLC, programmable thru HMI
- Water cooled platens
- Steam heated platens
- Oil heated platens
- Larger platen sizes
- Low pressure system
- Additional cylinder stroke
- Pressing speed control
- Contact gauge for quieter & more energy efficient operation
- Hydraulic part ejector
- High speed hydraulic package
- Digital display of clamp force
- Electronic force control
- Air-cooled heat exchanger
- WaterSaver valve for heat exchanger
- Work table
- Shuttle platens
- Lower sliding platens
- Mechanical eject
- Larger daylight opening
- Power operated safety gate (in lieu of standard manual gate
- T-slots or tapped holes in platen for mold mounting
- 7 day timer for heaters
- Cycle counter (with keyed reset)
- Chart recorder Light curtains
- Light curtains
- Extra heat zones in platen(s)
- Audible or visual alarms
- Mold heat temperature controllers and plugs
- Clamp area lighting
- 220, 380 or 575 volt operation
- UL, CUL or CSA configurations available